- June 9, 2023
- Posted by: admin
- Categories: General, Software, SprutCAM
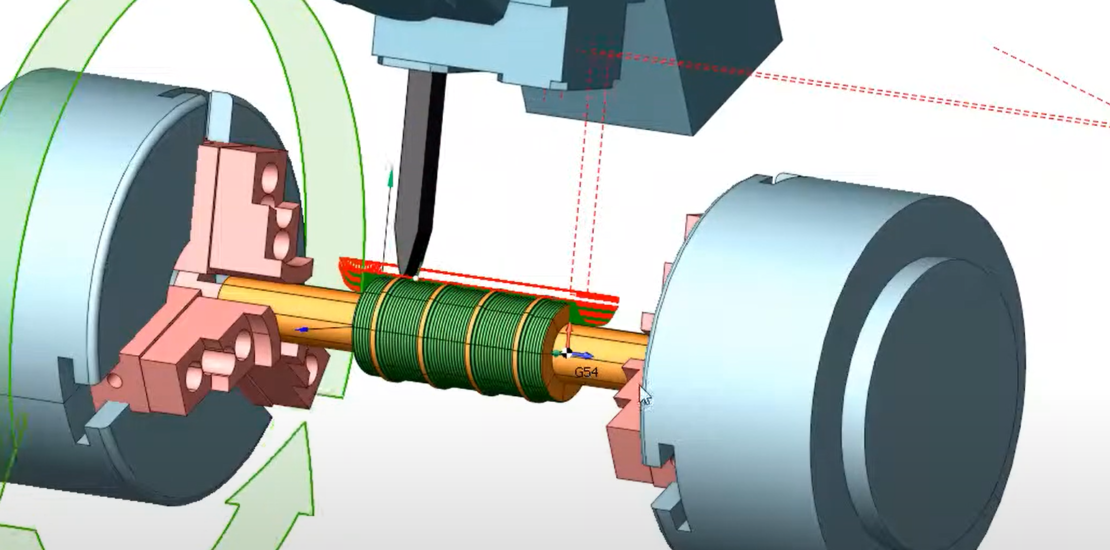
In the manufacturing industry, automation plays a very important role. Industrial automation contributes to overall performance by improving speed, standardization, and conformance to design specifications. The manufacturing industry utilizes robots for repetitive tasks, which streamlines the overall assembly process. SprutCAM Robot is a CAD/CAM and robot simulation application. It is used to program industrial robots for cutting, milling, painting, and welding, among other uses. SprutCAM is a unique offline programming software that includes:
- Toolpath calculation for any application
- Simulation
- Optimization for singularity and collision-free movements
- Post-processing
Toolpaths are generated based on the robot’s kinematics. The SprutCAM Robot kinematic scheme library includes a variety of robots from all major manufacturers, including Fanuc, Kuka, Staubli, Yaskawa Motoman, Toshiba, Mitsubishi, Nachi, ABB, and many others.
Programming Workflow:
Select the robot cell
The robot cell is a system that includes at least one robot and a controller. It does not require any special skills to assemble a robot cell. Simply select the component from the library and assemble a virtual robotic cell.
Import CAD model and select workpiece
Import the CAD model of the part to work and a workpiece.
Set parameters and calculate toolpath
Set the parameters and choose a toolpath strategy from a comprehensive set. After setting the parameter, the software will calculate the toolpath. An extensive range of toolpath strategies is available:
Roughing toolpaths:
parallel, equidistant, high-speed, adaptive roughing, roughing plane, roughing rotary machining, hole machining, and many more.
Finishing toolpaths:
finishing waterline, plane, scallop (3D constant step-over), morph, rotary machining, 5D surfacing.
Contouring toolpaths:
2D, 3D, and 5D contouring.
Special toolpaths:
Stone roughing, welding, heat treatment, sculpture milling.
Simulate and optimize
There is no need to switch applications while performing simulation operations. As a result of simulation and optimization, collisions between the workpiece and the tool are avoided, and as a result, the machining condition is improved. The robot axis map is a powerful tool for handling singularities, collisions, reach zone limits, and redundant axis movement.
Post-process
All major manufacturers are represented in the post-processor library. Once the simulation operation is complete, the software translates the toolpath location data into native robot command codes.
Applications
SprutCAM Robot used for the following applications:
milling (stone / wood / foam / resin), double spindle milling, wire cutting, deburring / trimming, grinding / polishing, cutting (plasma / laser / waterjet / knife), welding, painting / spray coating, dispensing, cooperative robotics, additive manufacturing, part to tool, rail / rotary, robot + CNC machine cooperation.